Interview with José Luis Sánchez, head of industrial development at AIDIMME
Information published by Javier García for Interempresas
José Luis Sánchez is head of industrial development at AIDIMME, a division that works to improve the manufacturing process efficiency, especially in the wood-furniture and metalworking sectors. In order to do so, the division uses traditional process-improvement tools in a consultancy format (process analysis, lean manufacturing-based techniques, developing improvement methods, customised training, etc.) or technologies focused on digitalisation processes, such as monitoring, automation, robotics, artificial vision, etc. The division is also part of the Plasma project, a demonstrator for 4.0 technologies that captures reliable data within two weeks to start the design of the scanning processes for smart or automated manufacturing. José Luis Sánchez explains what the digitalisation designing entails and how it can help a company, especially a SME.
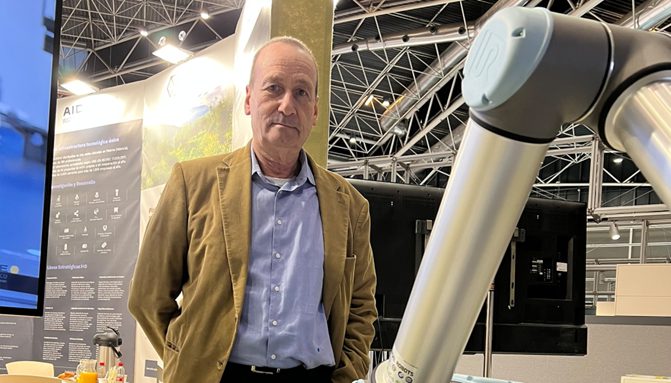
AIDIMME has initiated the Plasma system. What does it entail?
The Plasma project began in 2018 with the help of IVACE. It focuses on demonstrating the possibilities the digitalisation of these technologies offers in the manufacturing industry, especially in our reference field. Plasma has three demonstrators, two of them are portable and can be moved to the interested companies and the other is installed at AIDIMME – it reproduces a functional manufacturing line for personalised products.
What technologies does it incorporate?
One of the portable demonstrators has a complete process-monitoring system that can extract the information of any manufacturing process and show its operating status – to measure efficiency or analyse any relationship between variables that may interest the company. For example, it can measure product quality and relate it to the relevant variables in the process.
Another demonstrator is a collaborative robot installed over a mobile platform. It can be transferred to a company to evaluate the viability of the automation of any process. For example, it has been used to evaluate automatic machine loading and unloading, sanding and polishing procedures, piece unloading in transport systems, piece assembly, etc. The production line combines multiple technologies.
Which technologies?
RFID identification, collaborative automation focused on assembling parts in cooperation with a person, augmented reality for staff training, machine control integration in the production control system via OPC UA, additive manufacturing for the serial part production…
What type and profile of companies is it aimed at? Who can benefit from the advantages?
Plasma is at the disposal of any company interested in evaluating the integration of these technologies in their processes. There is no company-defined profile for using a demonstrator, though, compared to large companies, normally small and medium-sized enterprises have fewer possibilities to try this type of technology.
Which sectors does it focus on?
Originally it is aimed at the metalworking and wood-furniture sectors, although some technologies can be applied to any manufacturing sector.
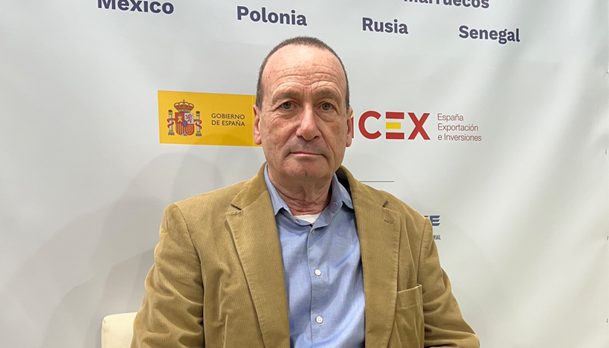
There has been talk of mass customisation. What can this platform do to this effect?
As I mentioned, the Plasma production line is designed to manufacture products that are completely personalised, so the implemented technologies are geared in this direction. For example, the fact that each manufactured product is identified individually allows the product itself to communicate directly with each process, automatically indicating the next operation that must take place. This enables the complete automation of the production flow, regardless of the lot size. Each product unit can be different from the previous and the next since the identifier will tell the machine what to do when it has reached a certain procedure.
This entails the machines to be able to adjust automatically and rapidly…
Yes, and by doing so a hundred equal units or a hundred different ones can be manufactured. And if in the assembly process there is a completely flexible machine – like a collaborative robot, a computerised quality-control system based on artificial vision – and is all complemented with an augmented reality system which indicates the specific packaging operation sequence it must carry out for each product. A completely flexible and adequate process is provided for personalised manufacturing or to produce larger or smaller batches (depending on the demand).
It is said that the system allows to evaluate the viability of a digital transformation process and to quantify the investment needed. How does it do it? What aspects does it consider?
Both mobile demonstrators can evaluate the viability of the technologies involved. Because they can be assembled directly into any process, they allow the own company to evaluate the advantages in the monitoring of the processes and the automation of some procedures.
What is this report about?
It analyses the gathered information in monitoring, or the cycle times achieved in the automation. From this data and the estimated investment or expenditures needed to implement the technologies, a payback period can be estimated. Therefore, these companies are provided with valuable information for the decision-making. The tests have not always acquired returns on investment that advise the implementation of one technology or the other.
How is this system being received?
At the beginning many demonstrations took place and the teams were nearly saturated, but now we are available to use the demonstrators in those companies interested in evaluating the digitalisation benefits, with a short waiting time.
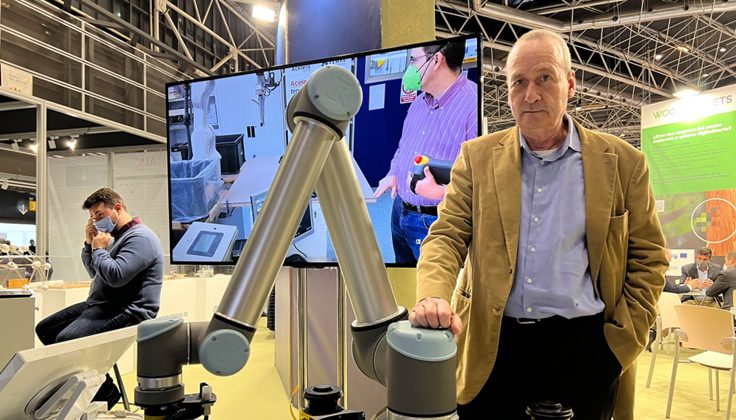
Sometimes it seems that in exhibitions and conferences, the solutions for the Industry 4.0 are presented and talked about, though the market is still not assimilating them. In other words, the supply and the demand are moving in different directions, and automation suppliers develop products and solutions that are not yet a reality in companies and production facilities in our country. How aware do you think the industrial sector is – especially the SME – about the new technologies?
I believe the industry is aware of the importance in digitalisation and knows many of the technologies that are currently available and which they can benefit from. But the solution developers’ pace and the industry’s pace are very different, due to the nature of each activity.
In the technological world, anyone who does not bring out an innovation every few months seems to be left behind. But the industry cannot modify constantly its methods, technologies or processes, because the clients demand stability and continuity. The changes must be carefully made and must not disrupt the essence of the business.
This does not mean that the industry cannot integrate the advances that are taking place in each field, but the path must be explored step by step, knowing the strategic priorities. I think this is still one of the main problems, because there are still many companies that do not question their priorities, even if we witness the constant change our surrounding is experiencing.
What arguments would you use to convince the industry about the advantages of the Plasma system?
The best way of convincing is by demonstrating in a practical way that a proposal – or in this case a technology – can work. On this basis, I invite them to experiment and, in view of the results, reach their own decision.
Access the Interempresas interview through this link.
Views: 69