Impresión 3D por fusión de lecho de polvo de polímero
La fusión por lecho de polvo de polímero es una técnica de fabricación 3D, que utiliza una fuente de calor (normalmente un láser) para sinterizar o fusionar las partículas de polvo atomizado.
Como ocurre con otros procesos de fabricación aditiva, se realiza capa a capa hasta completar la pieza.
Los sistemas de fusión de lecho de polvo de polímero utilizan, como su nombre indica, un polvo de plástico fino y crean formas 3D ddiferentes según el proceso que se utilice.
La tecnología más utilizada hoy en día es la conocida como Selectiv Laser Sintering (SLS).
Fases del proceso de impresión
Durante el proceso de impresión, el material en polvo se almacena en un tanque y se dispersa en una fina capa sobre la bandeja de impresión.
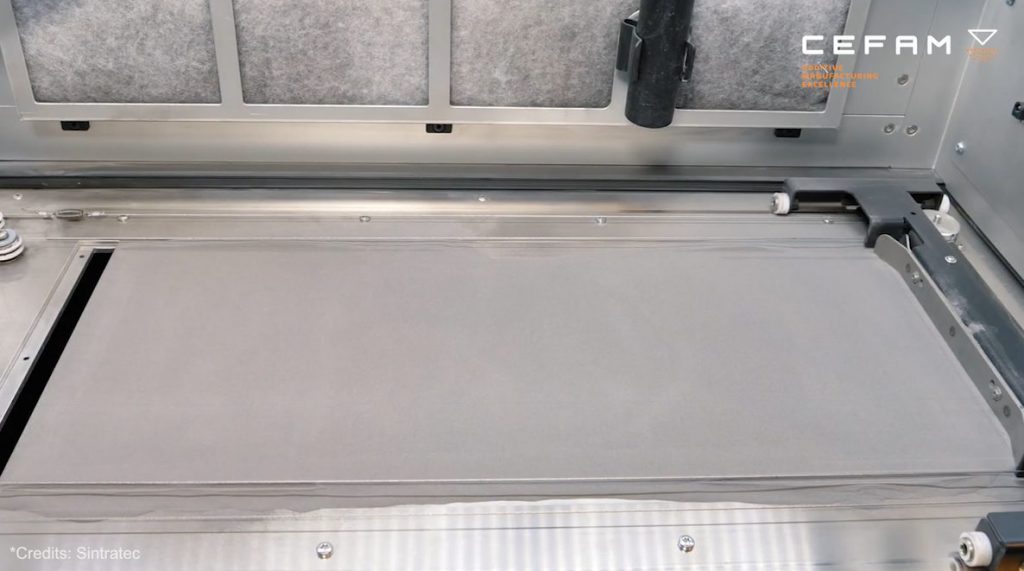
Para fusionar las partículas de polvo y formar un objeto sólido, la máquina precalienta el material, justo por debajo de su temperatura de sinterización.
Gracias a esto, las partículas no fundidas no necesitan mucha energía para sinterizarse juntas.
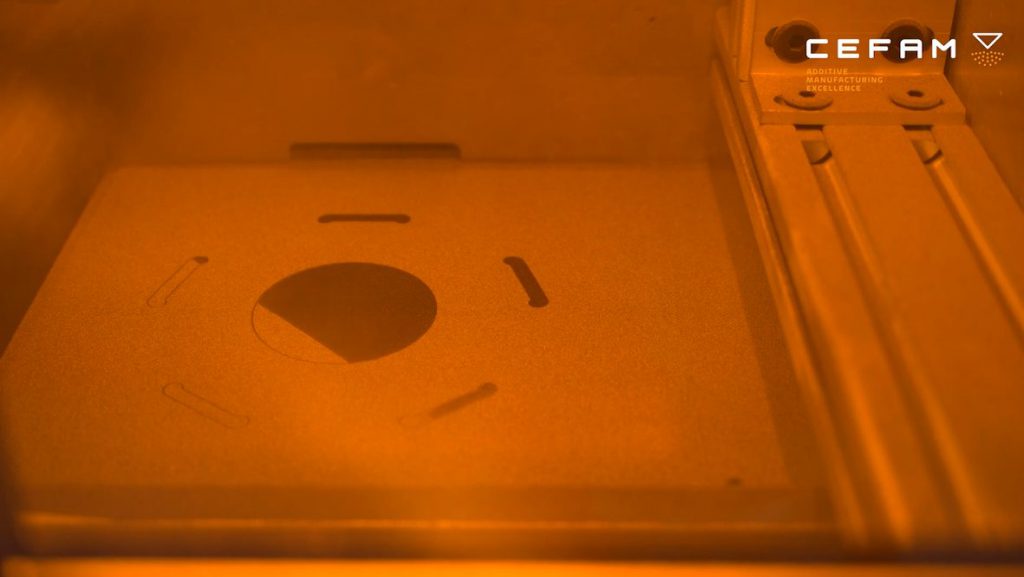
Esta energía adicional es aportada por un láser que fusiona secciones transversales de la capa que se está imprimiendo, para fundir el polvo en su lugar y formar la pieza tridimensional.
Principales ventajas de esta tecnología de fabricación
- El polvo que rodea las piezas impresas, y que no ha sido fusionado, actúa como soporte natural de las mismas.
Lo que significa que no es necesario un soporte adicional para crear geometrías complejas. - Esto permite otra ventaja, el llamado apilamiento o stacking, que significa que existe la posibilidad de apilar varios objetos, uno encima o dentro de otro, en un mismo volumen de impresión.
Una vez terminada la impresión, los objetos son fáciles de separar, ya que se imprimen individualmente dejando un margen de separación entre ellos. - Otra de las grandes ventajas de esta tecnología es que los objetos impresos son casi isotrópicos.
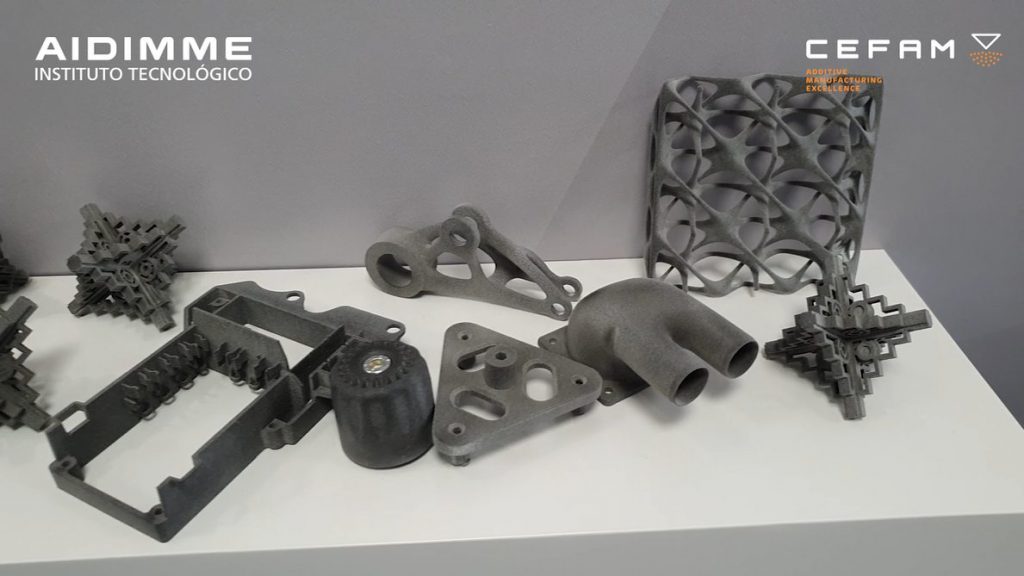
Sistemas propios de fusión de lecho de polvo de polímero
Cabe mencionar que, además del SLS algunos fabricantes han desarrollado sus propios sistemas de fusión de lecho de polvo de polímero.
Este es el caso de HP con su conocida tecnología Multi Jet Fusion (MJF) basada en un proceso de fusión de agentes múltiples.
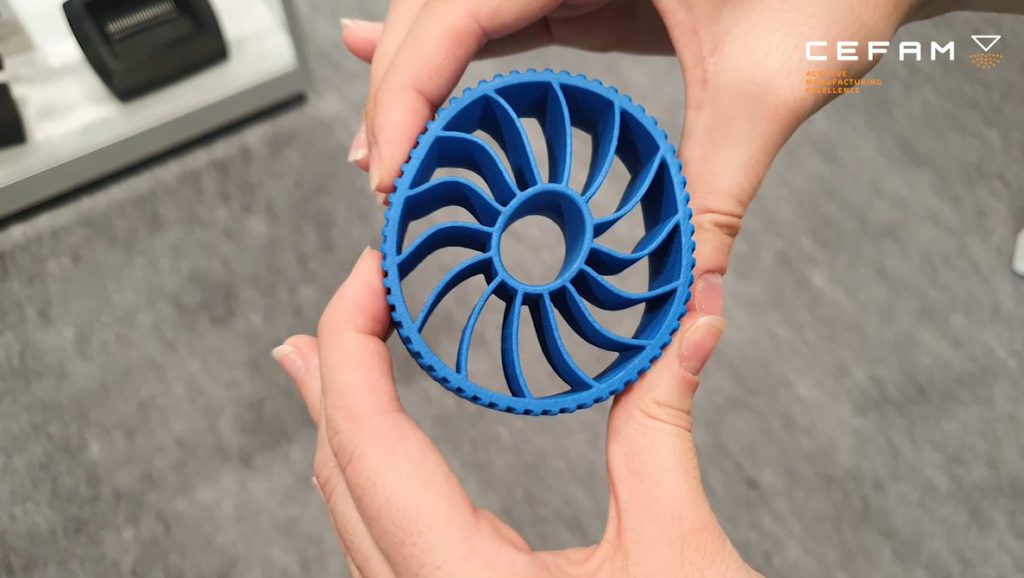
Durante la impresión se van aplicando agentes de fusión a las distintas capas de material que se van generando.
En términos de materiales estas máquinas emplean polímeros termoplásticos en forma de polvo, siendo el más común el polvo de nylon.
También podemos encontrar otros polímeros como polipropileno, el TPU y el TPE, si se requieren piezas con más flexibilidad.
En las tecnologías de fusión de lecho de polvo con polímeros es necesario realizar algún tipo de post-tratamiento.
Como las impresiones están rodeadas de polvo sin fusionar, los objetos salen de la máquina en un bloque de polvo apilado.
Para conseguir los resultados, el bloque debe separarse y eliminar el exceso de polvo de las piezas.
En este sentido, existen varias técnicas diferentes de post- procesamiento.
Las más comunes son: la eliminación de polvo por chorro de arena y el cepillado de alambre.

Una vez limpias, las piezas pueden utilizarse como tales o seguir siendo procesadas mediante otros sistemas de chorreado, volteo, recubrimiento o coloración.
Aplicaciones de la fusión por lecho de polvo de polímero
Hoy en día podemos encontrar todo tipo de maquinaria. Desde soluciones de escritorio para los entusiastas que quieren iniciarse en esta tecnología, así como otras más industriales destinadas a la producción en masa para los sectores más exigentes.
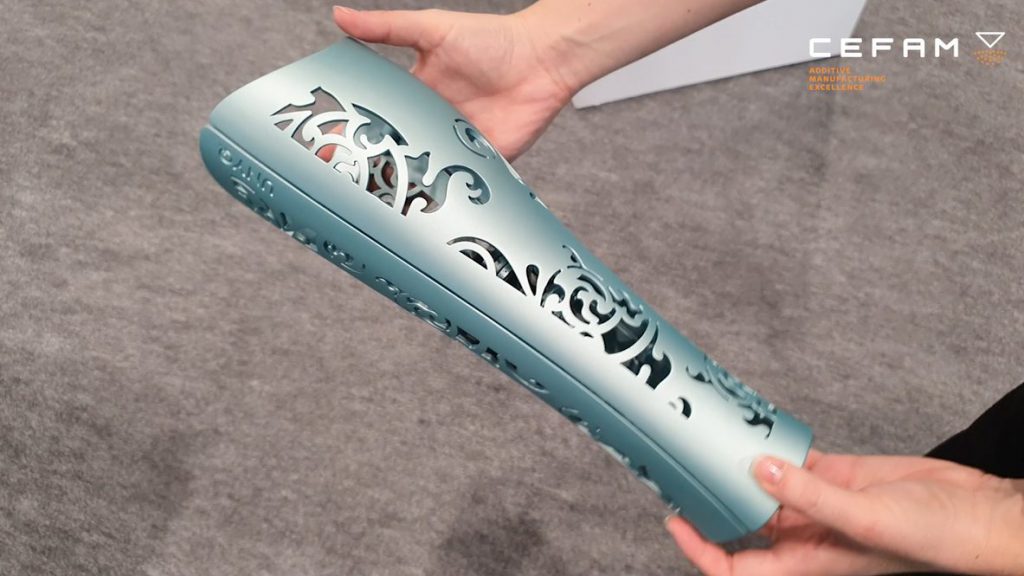
En términos de aplicaciones, la tecnología Power Bed Fusion se utiliza principalmente en ingeniería, gracias a sus propiedades mecánicas; su acabado cercano a objetos isotrópicos, su precisión y su capacidad para reproducir detalles.
Con el fin de optimizar cada proceso de fabricación, es recomendable imprimir por lotes y apilar lo máximo posible para evitar el desperdicio de material.
Además, al manipular el polvo y realizar el post-procesamiento, es obligatorio emplear equipos de protección individual (EPIS) para garantizar la protección del usuario.
Para más información contacte con AIDIMME.
Visitas: 355