Tecnología de fusión de lecho de polvo para piezas finales (PBF)
Las tecnologías basadas en fusión de lecho de polvo son tecnologías de fabricación aditiva.
Podemos dividir esta familia de tecnologías según utilicen un material u otro. Por ejemplo las que utilizan polímeros y las que usan metales.
En el caso de las que trabajan con metal destacan:
- Tecnología PBF-LB (Laser Powder Bed Fusion). Hace referencia a la fusión directa de metal por láser.
Se trata de un método de fabricación aditiva en el que se utiliza un láser para fundir, capa a capa, partículas de metal dispuestas en un lecho de polvo. - Tecnología PBF-EB (denominado también Electro Beam Melting). Es una tecnología desarrollada únicamente por ARCAM perteneciente a la empresa GE Additive.
Utiliza un haz de electrones para realizar la fusión del polvo.
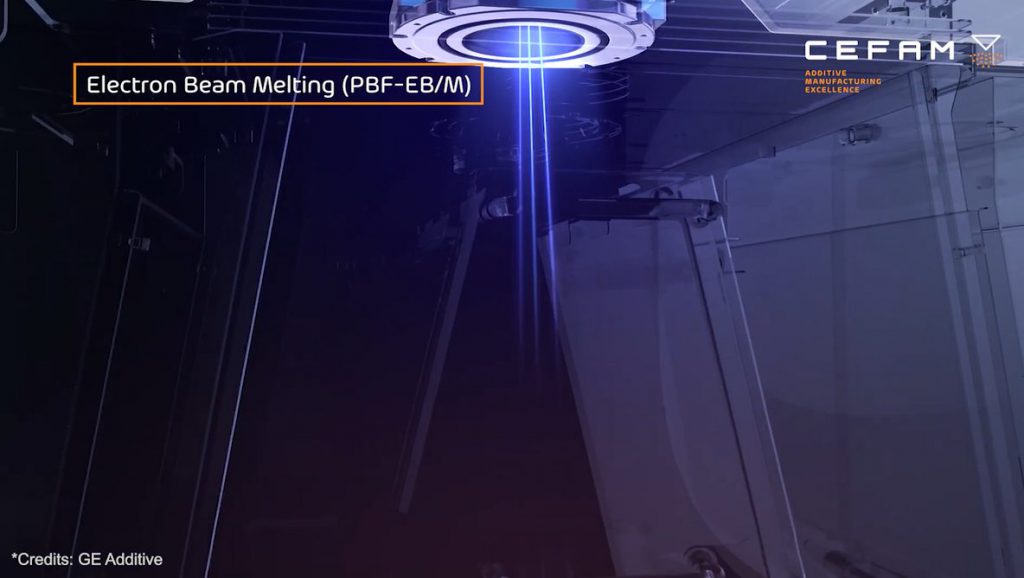
Una de las diferencias entre ambos sistemas de impresión 3D reside en la fuente de energía utilizada.
En una se utiliza un láser, y en otra un haz de electrones. Cabe destacar que el haz de electrones trabaja en vacío, y las de láser en una atmósfera controlada.
Piezas finales con el sistema de fabricación basado en lecho de polvo
El sistema de fabricación repite el mismo proceso hasta conseguir la pieza final.
Primero se calienta la bandeja de impresión hasta alcanzar la temperatura óptima de fusión
Esta temperatura dependerá de la tecnología y del material procesado.
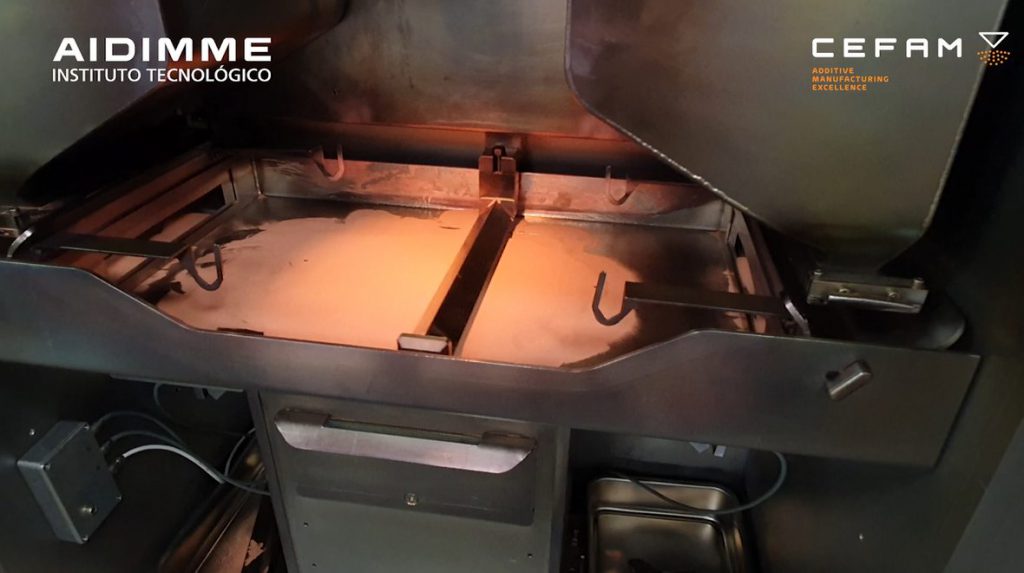
A continuación, una barra dispensadora aplica una fina capa de polvo metálico que recubre toda la bandeja.
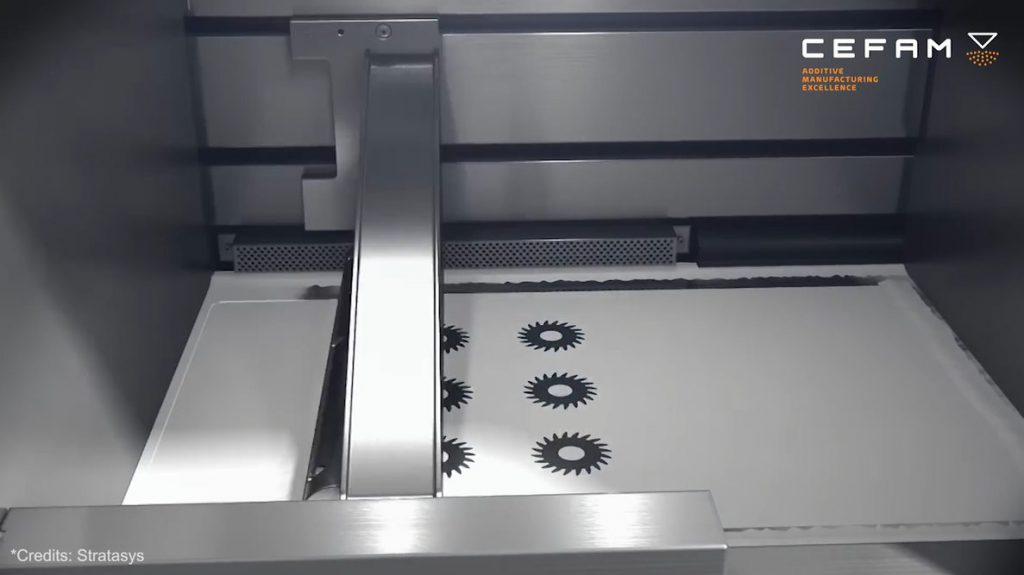
Después, la fuente de energía fusiona punto por punto las partes de la pieza, hasta completar la capa en cuestión.
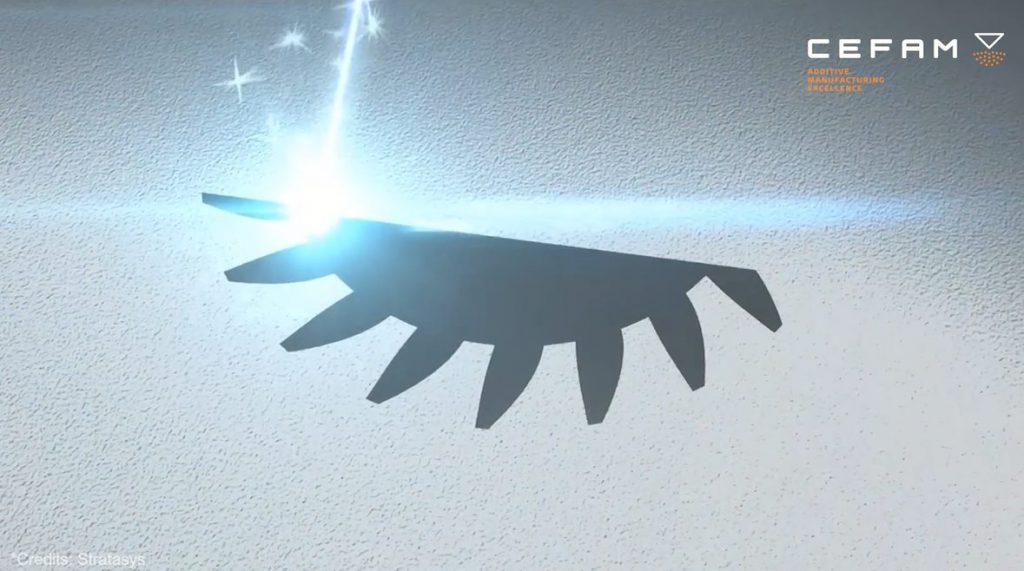
Una vez este paso ha finalizado, la bandeja de impresión desciende unos milímetros para dejar paso a la siguiente capa de polvo y comenzar de nuevo el proceso.
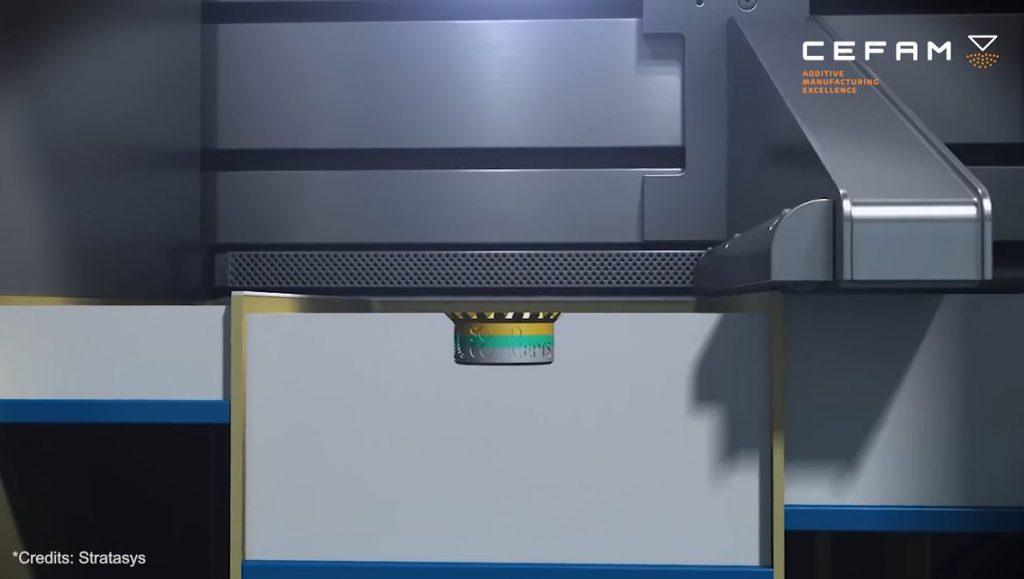
Si bien es cierto que no es obligatorio utilizar estructuras de soporte está altamente recomendado.
En este sentido, el término de “soportes” tiene dos funciones:
- La primera sería el anclaje de las piezas a la bandeja de impresión.
- La segunda la de evacuación del calor para no comprometer la integridad de la pieza o del material.
Estos materiales metálicos pueden ir desde acero inoxidable hasta cromo-cobalto, aluminio, cobre, aleaciones de titanio o de níquel, entre otras.
Estos sistemas requieren de ciertos pasos de post-tratamientos para retirar el polvo no fusionado de la bandeja de impresión.
A esto hay que añadirle la eliminación de los soportes, en el caso de que se haya recurrido a ellos, mediante métodos de corte, mecanizado o electroerosión por hilo.
Igualmente, las piezas finales pueden tratarse térmicamente para reducir las tensiones residuales y mejorar sus propiedades mecánicas.
Sobre todo en los sistemas basados en fusión por láser PBF-LB. Además, también se puede combinar con mecanizado CNC, o un proceso de pulido para ofrecer una mejor calidad de superficie.
Soluciones disponibles en el mercado
Debido a la complejidad de la tecnología de fusión de lecho de polvo cuando utiliza metales, las soluciones disponibles suelen tener un precio muy elevado.
Además, la precisión y calidad de las piezas finales hace que estas máquinas industriales sirvan para las aplicaciones más avanzadas dentro de sectores como el aeroespacial, el automotriz o el médico.
Algunos de los actores más destacados del mercado son SLM Solutions; Renishaw; Trumpf; Prima additive; EOS; G Additive, o 3D Systems, entre otros.
Al trabajar con las tecnologías PBF, LB o PBF EB, es altamente recomendable contar con el equipamiento adecuado a la hora de manipular las partículas de polvo metálico.
Esto también incluye la utilización de trajes EPI durante el post-tratamiento y la eliminación de polvo, ya que de lo contrario podría ser nocivo para la salud.
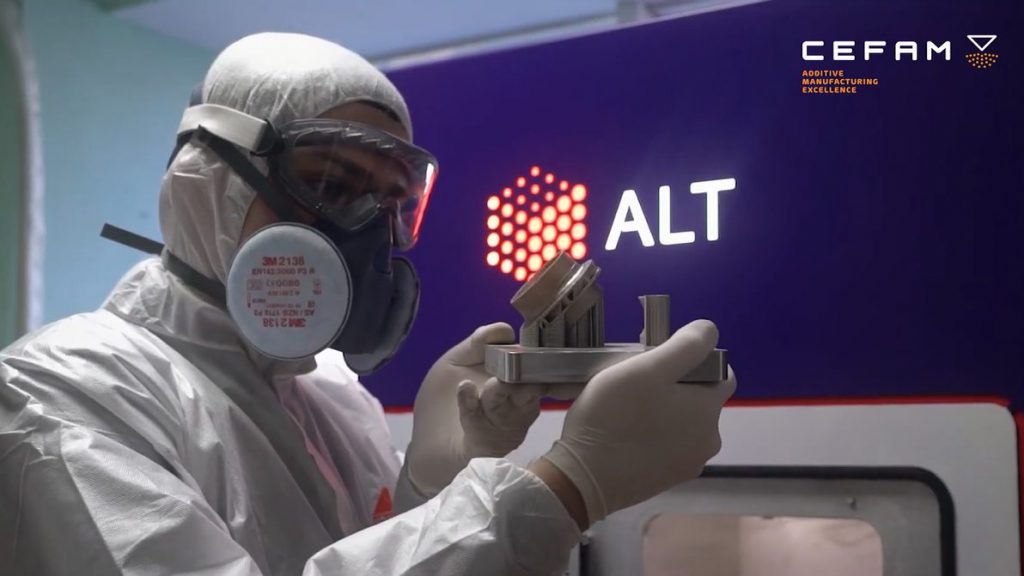
Además, es interesante realizar un diseño adaptado a estas tecnologías, así como recurrir a soluciones de software que integren herramientas de optimización topológica para conseguir reducir el peso final de las piezas, ahorrando tiempos y costes.
AIDIMME, junto a CEIT, CATEC y LORTEK, forma parte del proyecto CEFAM cuyo objetivo general es la creación de una red de excelencia en Fabricación Aditiva.
Puede obtener más información en la web de CEFAM.
Para más información contacte con AIDIMME.
Visitas: 564