Formación en metodología 5 ESES. La elección de la zona piloto
AIDIMME ha impartido a lo largo de 2018 cursos de mejora del puesto de trabajo en fábrica mediante la metodología 5 eses en las empresas Sarrimad, Maderas del Real, y Lagrama, asesorándoles en la implantación progresiva de éste tipo de herramientas.
Dentro del abanico de herramientas de la “filosofía Lean”, las 5 eses suponen una herramienta básica para cualquier proceso de mejora en el ámbito de operaciones. Por un lado su implantación aporta el orden físico (equipos, herramientas, materiales) necesario en cada puesto de trabajo, y por otro contribuye de forma clara y directa a la involucración de los trabajadores con la mejora continua de su puesto de trabajo, y de forma implícita con las tareas y procesos que en él se llevan a cabo.
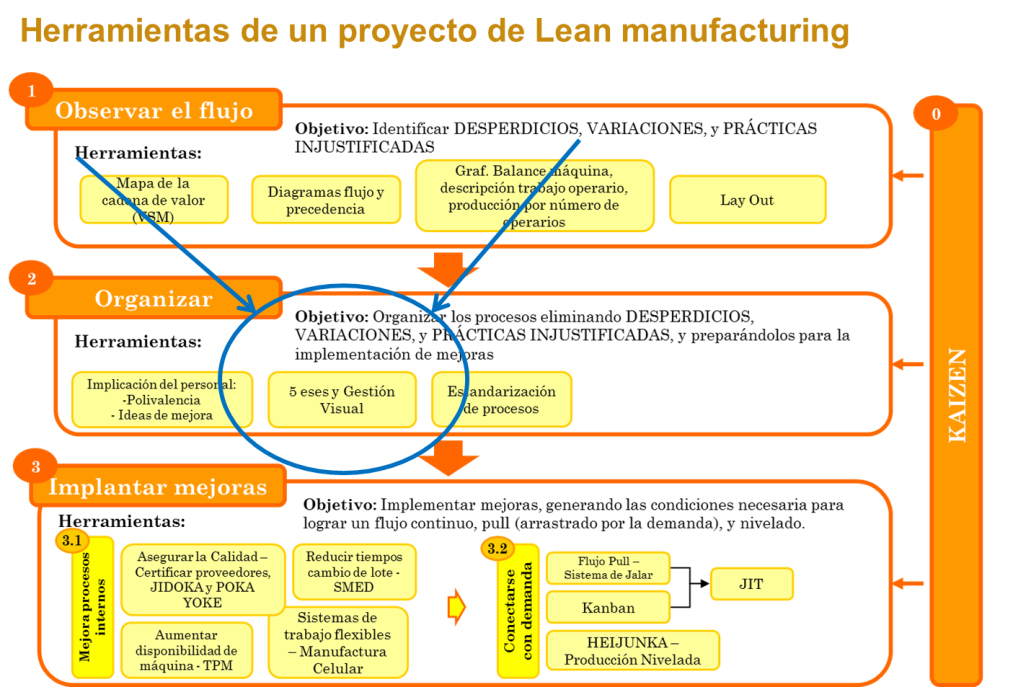
Conceptualmente la herramienta de las 5 eses no lleva consigo la aplicación de una teoría compleja. Se trata de aplicar 5 pasos, cada cual relacionado con una palabra japonesa que comienza por la letra ese (Seiri – Separar; Seiton-Situar, Ordenar; Seiso-Limpieza; Seiketsu-Estandarizar; Shitsuke-Hábito).
Pero justamente en su simplicidad radica una de sus barreras a la hora de aplicarla, ya que puede caerse en la tentación de “simplificar” la metodología dejándola solo en limpiar el puesto de trabajo y “pintar líneas delimitando pasillos” en el suelo.
La elección de la zona piloto donde comenzar un proyecto de 5 eses es clave a la hora de alcanzar el éxito en su implantación.
Por un lado, es importante elegir un área o puesto de trabajo donde las mejoras se puedan alcanzar rápidamente y a su vez se pueda visualizar la diferencia entre el “antes” y “después” de la implantación.
En procesos de fabricación en línea, con un flujo de producción alto y concentrado en unas pocas referencias, suele ser una buena opción comenzar allí donde el personal de mantenimiento debe actuar de forma continua (comprobaciones, mantenimiento preventivo, reparaciones, etc.) ya que suelen coexistir herramientas, recambios de máquina, etc., acumulándose herramientas y piezas innecesarias.
En un flujo por procesos, donde se fabrica un número de referencias diferentes muy elevado en lotes muy pequeños, merece la pena concentrarse en un área o sección del proceso total. Las secciones donde debe prepararse material para ensamblaje, y el propio montaje final del producto suele ser una buena opción. La correcta identificación de las piezas ya mecanizadas y pintadas, suele ser un reto donde las 5 eses pueden aportar la dosis de organización adecuada.
Por otro lado, la elección del piloto no depende solo el flujo del proceso. Las personas involucradas en el mismo deben ser claves para su elección. El proceso o línea escogida debe contar con trabajadores proactivos y con una motivación natural a cambiar, probar, y “hacer las cosas diferentes”. Es natural sentir cierto nivel de rechazo antes los cambios en nuestro entorno (en cualquier actividad de nuestra vida diaria, no solo en el trabajo), pero ciertas personas presentan un enfoque y actitud más positiva ante los mismos. Hay que tener en cuenta que la herramienta de las 5 eses no busca “culpables”, sino oportunidades de mejora, y propone una metodología estructurada para implementarlas.
En definitiva, si combinamos ambos factores (actividad y personal adecuados) habremos encontrado nuestra zona piloto donde comenzar nuestro proyecto de implantación de las 5 eses. Los resultados de la prueba piloto, deben de servir de muestra y experiencia al resto de procesos y personal de los beneficios que pueden llegar a alcanzarse con su implantación.
Para más información contacte con AIDIMME.